Avoid Being a Factory of Terror with These Manufacturing Safety Tips
If you work in an industrial environment, you’ve likely heard horror stories about on-the-job injuries, amputations or deaths. Sadly, most of these accidents could have been avoided if proper risk and safety solutions and adequate manufacturing safety training were in place. This blog intends to help your facility avoid becoming a factory of terror by providing manufacturing safety tips and best practices, as well as information on integrated safety devices, to help reduce risk in the manufacturing industry.
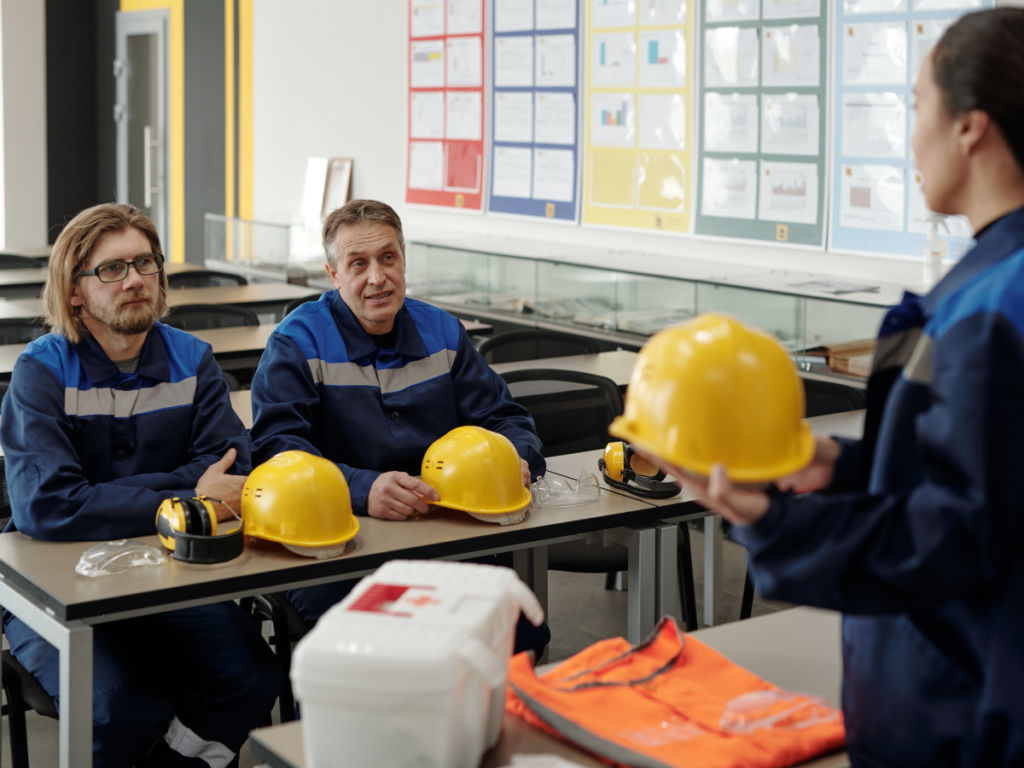
Risk in the Manufacturing Industry
Industrial facilities are active places filled with fast moving and potentially dangerous equipment, so it’s no surprise that the manufacturing sector has one of the highest levels of workplace injuries and deaths. According to the Bureau of Labor Statistics, the manufacturing industry experienced 373,300 total recordable cases of non-fatal injuries and illnesses and fatal work injuries totaled 341 in the year 2020.
And from October 2019 to September 2020, there were over 10,000 Occupational Safety & Health Administration (OSHA) violations in the sector, resulting in penalties totaling nearly $38 million. Not surprisingly, some of the top-cited OSHA violations were related to control of hazardous energies (lockout/tagout) and general requirements for all machines (machine guarding), which tend to be responsible for many of the manufacturing workplace injuries and carry some of the greatest risks in the manufacturing industry.
As a matter of fact, some statistics show that 80% of all manufacturing workplace injuries and fatalities are related to machinery accidents involving:
- Equipment not being locked out
- Untrained personnel
- Equipment not being shut off
- Failed interlocks
5 Manufacturing Safety Tips to Avoid Becoming a Factory of Terror
To prevent manufacturing machinery accidents, proper risk and safety solutions should always be in place on the factory floor, especially around fast-moving, heavy and dangerous manufacturing machinery.
The following five manufacturing safety tips will go a long way to preventing workplace accidents:
- Use personal protective equipment (PPE) where necessary: PPE should not only be available, but manufacturing safety training should be provided so employees know when and how to use it. PPE should also be inspected regularly to ensure that it is in good working order and any that is not should be replaced immediately.
- Provide manufacturing safety training: All employees should be trained in how to properly start, operate and stop the manufacturing machinery that they are responsible for using. Ensure that proper licensure is obtained, if necessary, before employees use a piece of equipment. And, as stated above, training should be provided to ensure correct use of PPE.
- Use appropriate safety guards and interlocks: Ensuring that equipment is properly guarded will help prevent machinery accidents. Employees should never remove or reach around guarding.
- Practice lockout/tagout procedures: One of the greatest risks in the manufacturing industry, energy hazards are a leading cause of workplace injuries and deaths in the sector. Consider any energy hazards that might be encountered and ensure that employees understand and use lockout/tagout procedures where maintaining equipment. Technicians and operators should always confirm that machinery is powered off and secured against unexpected motion before maintaining or working on or around equipment.
- Ensure a clean workspace: Slips, trips and falls are a major cause of serious workplace injuries – especially when an employee falls onto unguarded moving equipment. To prevent these accidents, workstations, floors and pass throughs should be free of debris, boxes, unused/spare equipment and parts, etc. Spills, leaks and messes should be cleaned up immediately.
Use Manufacturing Safety Equipment to Prevent Accidents
Because machine hazards are one of the leading causes of injuries and death on the factory floor, machine designers and safety engineers must follow OSHA standards to ensure the safety of employees. Integrated safety devices comply with OSHA regulations and are one of the best manufacturing industry safety solutions.
The following manufacturing safety devices offer protection for a variety of hazards:
Lockout/tagout solutions
These devices neutralize any potential energy in machinery to prevent unintentional equipment startups. They are available in a variety of solutions to suit any need, including locks with a single padlock to enforce manual locking and unlocking routines. Tags rely on coded colors and written details for visual indication of machine status. Hasps are used for isolation points where multiple operators or technicians may be required to allow operation.
Emergency stop devices
In case of an emergency, there should be a fast and reliable way to stop equipment from running. Emergency stops or E-stop buttons, switches, chains and ropes can be wired into equipment to override controls and cut off power to the machine. The devices should be placed in easy-to-access locations around each piece of equipment.
Two-hand controls and foot pedals
These devices allow operators to run machinery without getting too close to the hazardous parts. Two-hand control solutions require operators to use both hands to start the machine, reducing contact with pinch points and moving parts. If one or both hands are removed from the device, the machine shuts down to prevent injury. Foot pedals and switches are used in operations where hands-free operation is needed, such as on conveyors and presses.
Safety controllers, relays and modules
Relays and modules can control safety light curtains, safety interlock switches and safety mats. Safety controllers can be used to replace multiple safety relay units where there are multiple critical safety devices.
Machine guarding
Old-school guards and cages keep employees away from hazards, but many employees will remove or reach around them to keep production moving. Integrated safety devices such as safety light curtains create a sensor-based screen that stops machinery from running if an object breaks the beam. Laser scanners are another good solution as they will stop the process or machine if something breaches the light signal.
Safety interlock switches
Used with physical guarding solutions, safety interlock switches monitor mechanical guards to keep workers away from hazards. If a gate, door or panel is opened or removed, safety interlock switches will send a signal to the machine control system to stop the motion.
Safety mats and bumpers
Pressure-activated safety mats are used for the safe activation and deactivation of machines as they will only allow a machine to function if a user is standing on it. Safety bumpers stop motion if pressure or resistance is detected.
S
Manufacturing safety is essential to accident avoidance. Following safety best practices, providing manufacturing safety training and installing proper risk and safety solutions in compliance with OSHA regulations will help reduce risk in the manufacturing industry. Contact JHFOSTER today to learn about integrated safety devices and how they can help bolster manufacturing industry safety so your employees remain injury free and your facility does not become a factory of terror.