Choosing the Right PLC Programming Language for Your Automation Projects
While there are many PLC programming languages available for industrial automation projects, two of the most commonly used are ladder logic and function block diagram (FBD). Choosing which to use often comes down to personal preference or experience with one language or the other; however, each PLC language has advantages and disadvantages, which this blog will outline so you can choose the option that best suits the needs of your next automation project, as well as the experience of your programmer.
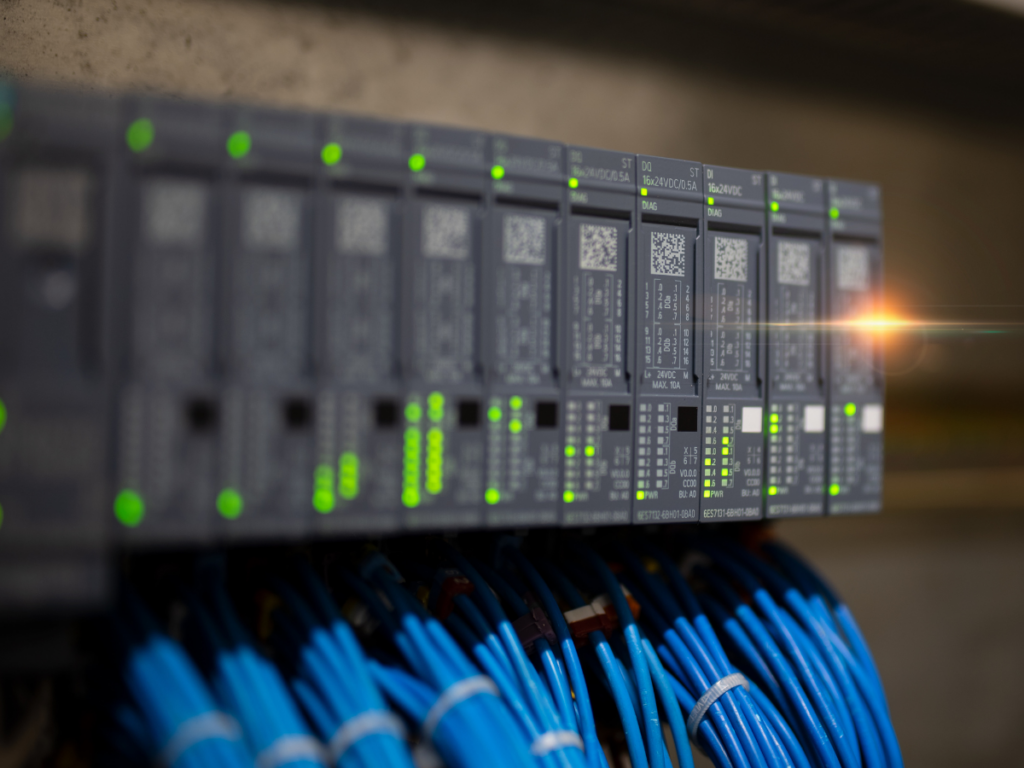
A Look at PLC Programming Languages
Before discussing the advantages and disadvantages of ladder logic and function block diagram languages, let’s first take a look at the basics of each.
Ladder logic, the very first PLC programming language to be used, is a graphical PLC language that looks a lot like electrical diagrams. As the name implies, this programming language uses rungs of ladder logic symbols, such as contacts, coils, timers, counters and functions. Each rung of the ladder represents an action that the PLC will execute. Ladder logic is easy to read, is used widely as a standard for machine automation projects and is supported by many PLC vendors.
Ladder logic works well for simple automation projects and is easy for electrical engineers and non-programmers who are familiar with relay logic to pick up, so it does not require a lot of PLC programming training. It is also flexible and easy to troubleshoot thanks to its graphical nature. Since its inception, ladder logic has evolved to become compatible with computers and Ethernet devices and can manage large amounts of data.
Function block diagram (FBD) is also a graphical programming language and it is used to join functions together to produce an output. Unlike ladder logic symbols, FBD employs lines and flags to represent variables in its graphical format, allowing users to quickly build a program by dragging, dropping and connecting different function blocks and variables.
Function block diagram allows users to create a visual representation and flow of the process with appropriate transitions between the instructions. This language is user friendly and intuitive and provides a lot of flexibility in a compact format. Users of this programming language do not need extensive programming skills or an electrical background.
Comparing PLC Programming Languages
Below we will explore the advantages and disadvantages of each PLC Language.
Pros and Cons of Ladder Logic:
PRO | CON |
Ladder logic is simple to implement and troubleshoot because it offers visual ladder logic symbols, so even someone with little knowledge of a specific process can understand the logic. | Ladder logic is cumbersome because it requires the use of many rungs and ladder logic symbols to express the same logic as other PLC programming languages. |
Ladder logic is modular in that it can be modified through the addition or subtraction of logic as each rung represents a separate condition. | It is easy to make errors by misplacing the order of rungs and ladder logic symbols. |
Ladder logic is suitable for simple, sequential tasks, such as motor control, interlocking and safety. | Ladder logic is unable to handle complex or parallel tasks, such as algorithms. |
Pros and Cons of Function Block Diagram:
PRO | CON |
FBD is a compact language. Users can accomplish in a single page of function block diagram what would require multiple rungs in ladder logic. | Function block text is most suitable for small implementations of a specific part of an overall project. For example, it’s commonly used to establish PID controllers. |
Using FBD comes naturally to most users due to the familiar drag-and-drop functionality. The ability to reuse code throughout programs also simplifies the process. | Execution of an FBD network is left to right, making it most useful for programming for continuous behavior, so FBDs are not the best method for solving sequencing problems. |
Function block text offers clarity of the data flow. The visual representation clearly shows how data flows through different function blocks. | Despite the clarity of the data flow, as the number of function blocks increases, the diagram can become cluttered and difficult to navigate, making it challenging to troubleshoot. |
When it comes to PLC programming languages for automation projects, there is no one-size-fits-all solution. Rather, the choice should be made on a project-by-project basis based on the complexity of the application, the comfort level of the programmer and the features of the hardware. For more assistance in choosing a PLC language, please reach out to Celco, a Tavoron company.