Leveraging Industrial Chillers for Precise Temperature Control
Manufacturers across a broad range of industries rely on industrial chillers to provide precise temperature control and cooling of critical processes while also improving product quality, reducing operating costs and increasing productivity. These energy efficient and cost-effective industrial cooling systems are available in different types and sizes to suit just about any application in which accurate temperature control is a requirement of production. This blog will explain the various types of industrial chillers and highlight a case study that demonstrates how modern industrial chillers can provide superior temperature control while maximizing throughput and minimizing expenses.
What is an Industrial Chiller?
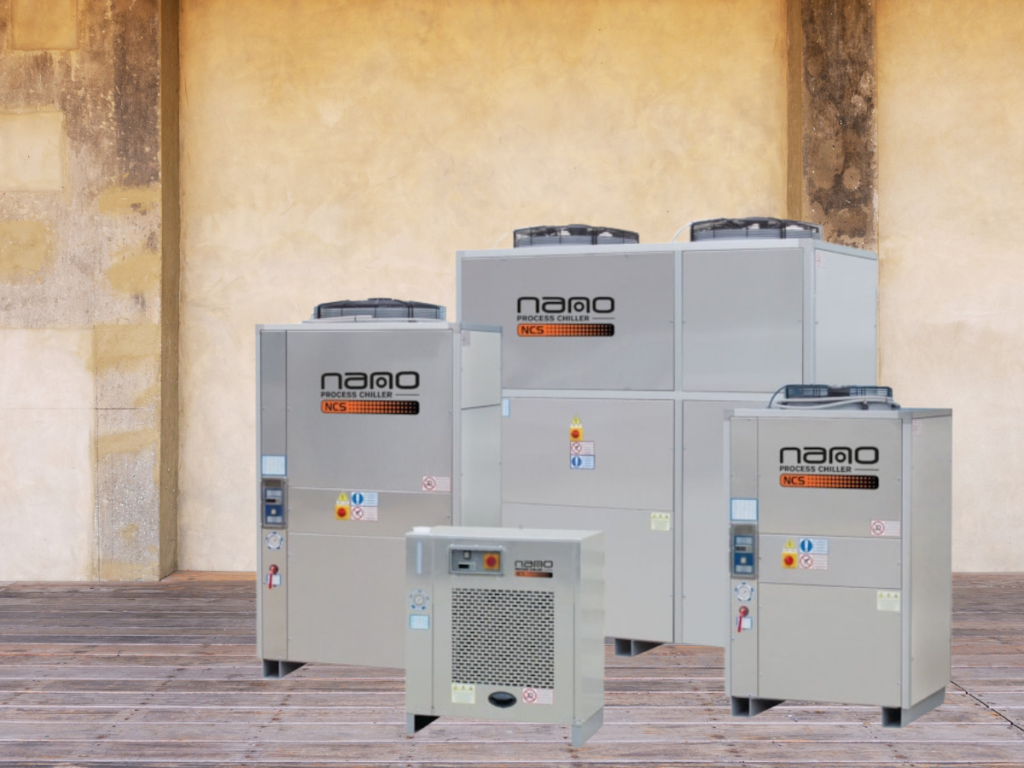
In the simplest terms, a chiller is a piece of industrial cooling equipment that cools processes down by removing heat from a liquid or a space and transferring that collected heat to a cooling medium (usually air or water) before expelling it. It’s important to note that while industrial chillers are used to cool to a precise temperature, they do not produce cold air like air conditioners or refrigeration systems, rather they circulate liquid cooling agents through the coils of the unit to absorb heat,
reduce the temperature of the cooling agent and then finally release it elsewhere, effectively and efficiently lowering the temperature of the process being cooled.
In manufacturing, industrial chillers – often called process chillers – play a critical role in achieving and maintaining the exact temperature required for production in applications where consistent cooling is crucial to the process or product quality. Industrial chillers can also be used as heat transfer equipment if heated water is circulated through the coils inside the chiller unit and then transferred into another tank. When properly controlled, industrial chillers provide precise temperature control in an extremely efficient and cost-effective way.
As such, these industrial cooling systems can be found across a broad range of industries, including plastic injection molding, food processing, pharmaceutical production, medical device manufacturing and power generation plants.
Industrial chillers are used in a range of industrial applications, including:
- Plastic processing
- Cooling water systems
- Dairy processing
- Meat processing
- Brewing
- Food and beverage processing
- Water treatment
- Chemical processing
- Pharmaceutical processing
- Freezer rooms and cold storage
- Water treatment
- Power generation
- Metal finishing
- Electric battery production
Types of Industrial Chillers
There are two main types of industrial chillers:
Air-cooled industrial chillers use ambient air to remove heat from the refrigerant in the condenser before condensing and recirculating it. Air fans are typically attached to the chiller unit to make the cooling process more effective and efficient. Air-cooled chillers are most suitable for applications where the discharged heat will not impact production as they may produce heat in the area. This type of industrial cooling equipment is suitable for smaller areas and is inexpensive to install.
Water-cooled chillers use water from an external source, often a cooling tower, to cool the refrigerant in the condenser. After dissipating the heat, the refrigerant is recirculated back into the system. Water-cooled industrial chillers offer high levels of efficiency, but require additional cooling water towers, tanks and pumps, so they may be more expensive to install and may not be suitable for areas where water restrictions are in place.
Using an Industrial Chiller for Precise Temperature Control
The following case study demonstrates how a modern, efficient industrial chiller not only cools to a precise temperature, but also improves productivity and reduces costs.
A few years ago, Coppertail Brewing Company, a growing microbrewery, was forced to acknowledge that its existing industrial chiller was unreliable as it had begun to require costly and time-consuming maintenance on a weekly basis to keep it up and running. Despite these efforts, frequent outages still occurred at least once or twice per quarter and could last for one to two days each time, costing the brewery $20,000 in lost product for each day production was down for a total loss of $80,000 to $320,000 per year in lost product, sales and lost productivity.
The brewery relies on “crash cooling” – a process that entails rapidly cooling the beer to near freezing temperatures to clarify the product before bottling. However, the cooling requirements varied from product to product, tank to tank and season to season, but due to the typical operation of the facility, the brewery had to run its industrial chiller at full load at all times during production and was unable to cycle off a compressor, regardless of demand, making energy consumption extremely high.
It became obvious that the brewer needed a more energy efficient and reliable industrial cooling system to handle the facility’s 16-hour, five-day operation, as well as anticipated production increases.
Nano Purification Solutions proposed the installation of a Nano model NCS-1004-US, a 43-ton, air-cooled, cycling industrial chiller with four 21 kW compressors and two cooling circuits. The chiller can run reliably at 20%, 50%, 75% and 100% of load while reducing amp draw and inrush current, which allowed Coppertail to reduce its chiller operating costs by 25%.
The new roof-mounted chiller was installed and currently provides chilled water to eight fermentation tanks and three finishing, or bright, tanks. Expansion plans call for the brewery to produce beer in 20 tanks in the future.
When calculating cost savings, the brewer determined that each of the 11 crash-cooled tanks require about 10 kW of refrigeration to crash cool the product from 70°F down to between 27°F and 30°F. With the old chiller, three tanks had to be offline before it was possible to shut down a refrigeration compressor; however, the new chiller can shut down compressors and save additional costs when a tank or two is offline.
This is a significant savings as the new unit is estimated to save 21kW for every two tanks taken offline. In addition, the new chiller with its additional capacity can process eight to ten tanks at a time, increasing capacity while reducing the cost of electricity. Further use of the new chiller may provide an additional energy savings of 5% thanks to the efficiency of the rotary scroll compressors and the use of no-frost heat exchangers.
As seen in the above case study, using a modern, well-controlled efficient industrial chiller can provide not only precise temperature control for critical processes, but also cost savings, energy efficiency and the ability to increase production. For more information on selecting the best industrial chiller for your application or to learn about Nano Purification Solutions can help with your industrial cooling needs, please reach out to JHFOSTER, a Tavoron company.