3 Things to Know When Sizing an Air Compressor
Properly sizing an air compressor can make you feel like Goldilocks – one air compressor may be too big (leading to increased operating costs due to wasted energy) and another may be too small (resulting in inadequate airflow to equipment and problems with production). So, how do you find the air compressor that is “just right” for your facility? This blog will provide three essential things to know when sizing an air compressor.
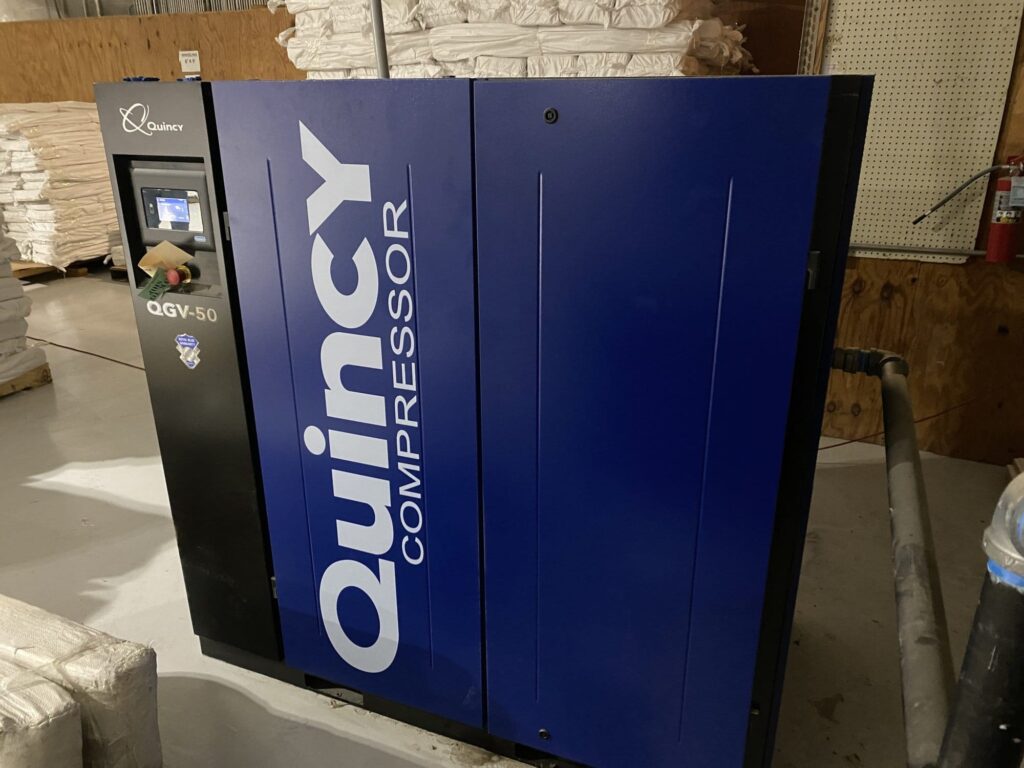
Before starting, it’s important to recognize that unlike most other industrial equipment, horsepower is not the main specification when sizing an air compressor. Rather, air compressor sizing is based on airflow, duty cycle, and pressure requirements, which can vary greatly from facility to facility, meaning air compressor sizing is not a one-size-fits-all proposition.
So, to select the most appropriate air compressor and ensure properly functioning equipment and maximum energy efficiency, you will need to determine the following:
1. Airflow Requirements: Airflow Requirements: Airflow requirements refer to the necessary airflow, which is the volume of air that an air compressor can provide in a given time period at a given pressure. This is measured in cubic feet per minute, commonly referred to as cfm. Airflow requirements must consider peak demand periods, compensation for inevitable air leaks and future growth. The suggested method to determine an accurate cfm, therefore, is to first locate the cfm requirements for each tool in the facility that will be used simultaneously and determine the sum of these cfm ratings. This figure will be the MINIMUM airflow that the compressor must be able to provide. After finding the minimum cfm, experts advise adding an additional 25%. For example, if the minimum total airflow was determined to be 100 cfm based on the capacity of the plant, a compressor with a specification of 125 cfm would be the most suitably sized air compressor for the current needs, as well as high demand periods, leaks and future expansion.
2. Duty Cycle & Percent Capacity: Duty cycle is usually applied to piston type compressors, the duty cycle is the amount of time that the compressor can supply consistent pressure (psi) and flow (cfm), which determines how frequently an air compressor can be run over a certain period of time. Knowing the duty cycle is the second step in sizing an air compressor and can be found using the following calculation: time on/(time on + time off) = Duty Cycle Percentage. So, if an air compressor has a 2-minute total cycle time and runs for 1 minute during that cycle (1 minutes/2 minutes = 0.5%), it has a 50% duty cycle time. This means it will deliver consistent pressure and flow for 1 minute and will need to rest for 1 minute before it can again supply pressurized air. This is important knowledge for air compressor users as it allows them to determine whether an air compressor can adequately meet their air needs without overworking. To determine your duty cycle needs, log your current tool usage per day and seek an air compressor with a duty cycle that meets those needs.
Percent capacity is usually applied to rotary screw or other types of rotary compressors designed for continuous duty. For these types of applications, it’s important to determine your maximum, average and minimum cfm flow requirements, as well as the amount of time the compressor will be operating in each range. For example, if your peak demand is 500cfm, but the compressor will spend most of its time running at an average of 200cfm, a variable speed drive type compressor will most likely be your best option.
3. Pressure Requirement: Pressure refers to the pound-force-per-square inch gauge (psig) that the air compressor will deliver. To determine the appropriate psig for your facility, find the tool or equipment with the highest amount of pressure required and use this as a baseline measurement. For this calculation you do not have to find the sum of all of the psig values in the facility, instead simply use the psig value of the tool that requires the greatest amount of pressure.
While these are the three most important criterion when sizing an air compressor, there are many other considerations and factors that influence sizing, such as the air compression system layout (compressors that are further from the endpoint may need a higher psig), the proper use of air tanks or receivers or the use of a single piece of equipment, such as an industrial baghouse, with a greater-than-average psig (the additional pressure may damage other equipment in the facility, which may require the use of regulators for other equipment or the use of separate, smaller high pressure air compressors may be desirable), as well as how shifts are operated and high demand periods
Unless your application is cut and dry, it may be beneficial to conduct an air audit to determine what size air compressor is most suitable for your operation. As a bonus, an air audit can also help determine the best configuration for the air compression system and other ways to optimize energy usage and the performance of your new air compressor. Air compressor suppliers, such as JHFOSTER, can assist you with air compressor sizing, as well as conducting an air audit.